Testing am Prüfstand, Teil 2
Die Prüfung der mechanischen Komponenten wie Antrieb, Fahrwerk oder auch Karosserie auf den Prüfständen war früher mehr oder weniger eine Standardaufgabe, hat sich aber in den letzten Jahren auch enorm weiterentwickeln müssen.
Hier bezogen auf die PKW Antriebe hat das Ganze in den 90er Jahren mit den automatisierten Getrieben begonnen. Bis dahin wurden die Antriebstrangkomponenten streng separiert getestet, der Verbrennungsmotor am Motorprüfstand und das Getriebe am Getriebeprüfstand. Da sowohl beim Verbrennungsmotor aber auch beim Getriebe immer mehr Intelligenz in deren Funktionalität sprich in deren Steuergeräte eingearbeitet wurde hat man erkannt, um den Treibstoffverbrauch zu senken bzw. den Wirkungsgrad des Fahrzeuges zu erhöhen es Sinn macht, die beiden Systeme in Echtzeit miteinander kommunizieren zu lassen. Nur im optimalen Zusammenspiel der Systeme lässt sich ein effizienter, verbrauchsoptimierter und letztendlich auch ein extrem hoher Fahrkomfort realisieren.
Der ganze Antrieb wurde in diesem Jahrzehnt mit der Hybridisierung noch um mehrere Stufen komplexer, denn mit dem Einzug des Elektromotors und dem dazugehörigen Batteriemanagement kommen noch zusätzliche Komponenten ins Spiel die interagieren müssen. Die Effizienz dieses komplexen Antriebssystem bekommt einen noch höheren Stellenwert da die elektrische Reichweite aktuell das Thema ist bei den elektrifizierten Fahrzeugen.
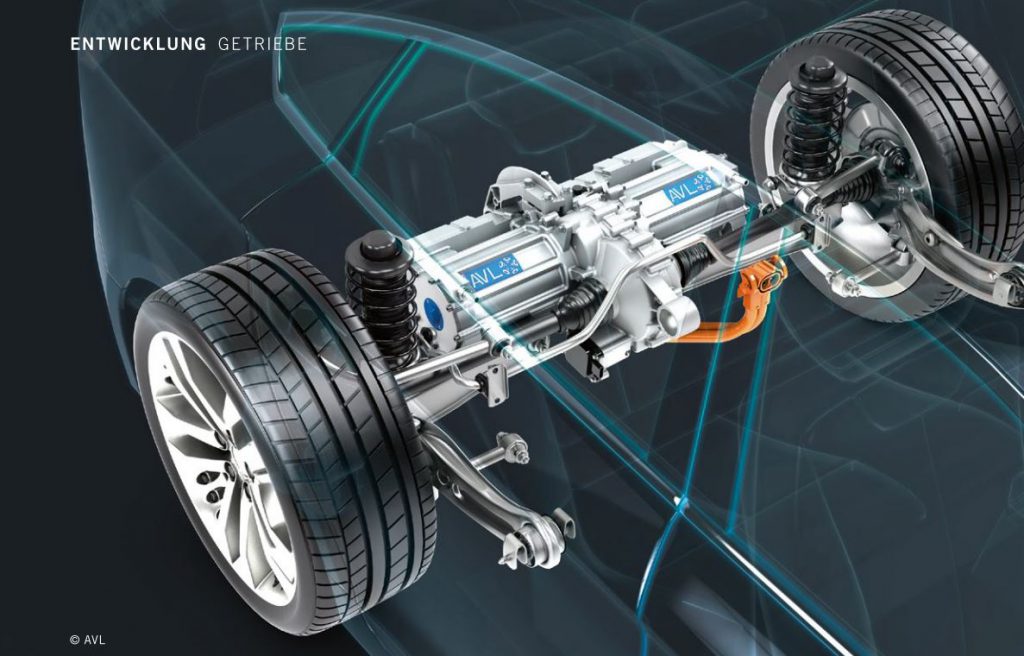
Aktuell befinden wir uns in der Entwicklung der reinen Elektrofahrzeuge. Auch hier stehen die Prüfstandsbetreiber wieder vor neuen Herausforderungen; das sind die hohen Drehzahlen der elektrischen Antriebsmaschinen (E-Maschinen).
Hier zum Vergleich: Ein klassischer Verbrennungsmotor dreht mit ca. 5.000 – 6.000Upm, die aktuellen E-Maschinen im Bereich von 20.000Upm. Die E-Maschinenhersteller wären auch in der Lage E-Maschinen mit 30.000Upm und höher herzustellen. Die Herausforderungen liegen hier ganz einfach an den hohen Antriebsdrehzahlen vor allem diese auf einem Antriebsstrangprüfstand über hunderte von Stunden Dauerlauf sicher zu stellen.
Dem Ganzen werden nun, wie schon erwähnt, die Validierung der Assistenzsysteme hinzugefügt. Vor allem muss auch berücksichtigt werden wie diese Assistenzsysteme auch das Verhalten und die Lebensdauer der Antriebstranges beeinflussen.
Auch hier arbeiteten viele OEMs, Zulieferer und Prüfstandshersteller daran diese gesamtheitliche Validierung der Systeme auf den einen hoch komplexen, oder auf die „einfacheren“ Subsystem-Prüfstände zu verlagern.
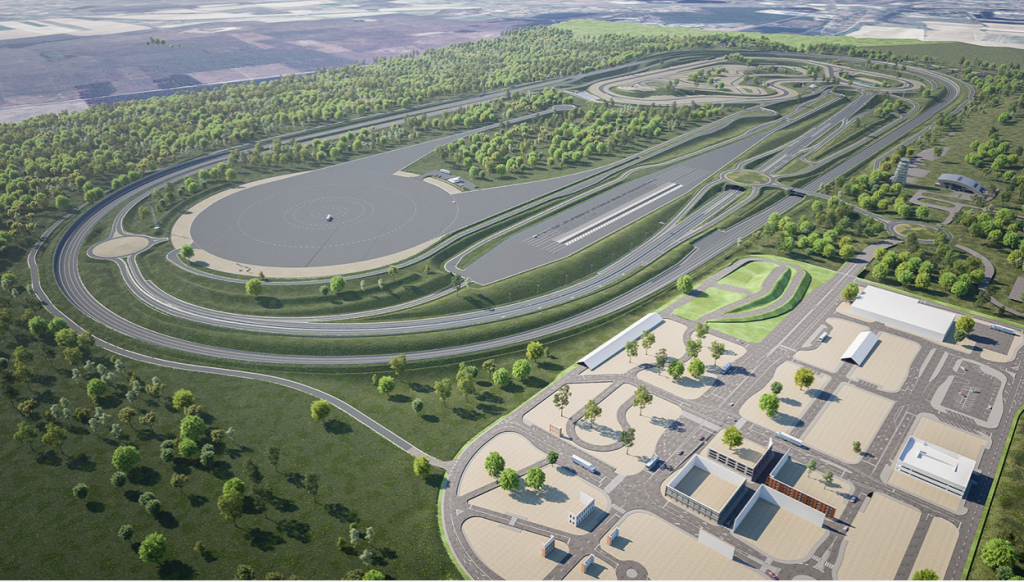
Da das aus heutiger Sicht noch etwas dauern wird diese gesamtheitliche Systemvalidierung zu 100% auf Prüfstände zu verlagern, werden aktuell Teststrecken auf allen Kontinenten hochgerüstet um realistische „Umgebungsbedingungen“ für die Validierung der ADAS zu schaffen. Hier werden auf Testgeländen Bereiche von Städten und Straßen abgebildet um die Systeme in einer sicheren Umgebung testen und validieren zu können. Um beispielhaft ein ganz neu dafür geschaffenes Testzentrum zu nennen; die ZALA ZONE in Ungarn, wo hier auf 265 Hektar Fläche ein komplettes Testzentrum auf die Beine gestellt wurde.
Link: https://zalazone.hu/en/.
Das alles auf einen Prüfstand abzubilden ist die nächste Stufe der Herausforderung an die Prüfstände. Die Anforderungen an die Prüfstände der Zukunft sind enorm, um so komplexer die Aufgabenstellungen werden umso größer sind die Anforderungen an den Prüfstand.
Nichtsdestotrotz werden weiterhin „einfache“ Prüfstände vonnöten sein um die Subsysteme zu erproben und validieren. Bei diesen sog. Dauerlaufprüfständen ist es wichtig die Komplexität möglichst niedrig zu halten um einen störungsfreien, automatisierten Betrieb über 24 Stunden und 7 Tage zu gewährleisten.
Umfangreiches Wissen und Erfahrung sind vonnöten um hier vorne dabei zu sein.
Sinamono kann dazu mit den vorhandenen Experten eine adäquate Unterstützung anbieten um Dienstleister, Zulieferer oder auch Prüfstandshersteller in ihren Aufgaben zu unterstützen.