In der Werbung und auch in sehr vielen technischen Zeitschriften wird zunehmend von Fahrzeugen aus China berichtet. Meistens berichten sie über das futuristische Design der Fahrzeuge, was sie so alles im Vergleich zu europäischen Autos können und dass diese zu einem Preis zu haben sind, den die Automobilindustrie in Europa nicht darstellen kann.
Natürlich lese und höre ich diese „Werbung“. Da ich aber schon sehr lange in der Fahrzeugentwicklung tätig bin und seit geraumer Zeit mit Fahrzeugzulieferer (Tier 1, Tier 2) zusammenarbeite, die auch in China entwickeln und produzieren lassen, habe ich ein etwas differenzierteres Bild bekommen wie sich die Entwicklungsstrategien in China, vor allem bei den modernsten E-Fahrzeugen, gegenüber den mir bekannten etablierten Märkten im Westen unterscheiden.
Vorweg möchte in festhalten, dass ich weder die eine noch die andere Strategie für gut oder schlecht halte. Ich möchte lediglich meine Wahrnehmung zu Unterschieden in den Entwicklungsphilosophien europäischer und asiatischer OEM und die Auswirkungen auf Entwicklungszyklen, Qualität und Preis mit Ihnen teilen.
Sehr oft bekomme ich zu hören, dass die Chinesen in der Entwicklung viel schneller und billiger sind. Sie haben schneller die Prototypen fertig und liefern viel schneller Ergebnisse, als wir hier im Westen. Diese Meinung wird vor allem von Personen aus dem mittleren Management und vom Vorstand vertreten.
Dem ist zunächst einmal wenig entgegenzusetzen. Erkennbar war und ist, dass chinesische Entwicklungszentren tatsächlich viel schneller Ergebnisse liefern, als ihre Konkurrenz in Europa. Aber, …
Hierzu gibt es aus meiner Erfahrung ein sehr viele Aber. Auf was bezieht sich das Ergebnis? Wie waren die Parameter eines Tests? War dieser Test sinnvoll, basierend auf der Qualität des Prototyps? Gibt es vergleichende Simulationsergebnisse? Und vieles mehr. Wenn man diese Fragen in Richtung China stellt, – und ich beziehe mich in meinen Ausführungen auf die Diskussion mit chinesischen Ingenieuren, mit denen ich zu tun hatte,- stellt man sehr schnell fest, dass es keine Antworten gibt.
Vielfach musste ich feststellen, dass es vor allem bei den nicht etablierten OEMs aus China keine standardisierten Entwicklungsabläufe gibt. Selbst Lastdaten zur Bauteilentwicklung sind nicht vorhanden sind. Aus diesem Grund, sozusagen als Teil des Lösungsansatzes, beauftragen diese OEMs erfahrene Zulieferer in Europa oder den U.S. mit der Entwicklung des Bauteil oder der Komponente. Verbunden mit dem Auftrag ist die unausgesprochene Hoffnung, dass dieser Zulieferer ohnedies weiß, wie er seine Komponente zu entwickeln hat und die entsprechenden Daten zur Verfügung stellt. Aber hier beißt sich die Katze in den Schwanz.
Wenn der OEM nicht weiß, welche Belastungen auf das Bauteil oder die Komponente in seinem Zielfahrzeug wirken, dann fehlen die Eingangsgrößen für die Entwicklung beim Zulieferer. Diese können auch zumeist (noch) nicht durch Erfahrung ersetzt werden, da das Fahrverhalten chinesischer Kunden mit e-Fahrzeugen unbekannt ist, Informationen über die Konfiguration des Antriebskonzepts oder Lastdaten aus dem Fahrzyklus fehlen.
Jetzt kommt noch die chinesische Kultur und tradierte Umgangsformen ins Spiel. Der Zulieferer sollte aus Höflichkeit seinem Kunden, dem OEM, keine detaillierten Fragen stellen, wenn Gefahr besteht, dass dieser dieser nicht beantworten kann. Er steht in der Hierarchie unter dem Auftraggeber und muss streng darauf achten, dass alle Seiten zu jedem Zeitpunkt Ihr Gesicht wahren können.
Was passiert jetzt? Die chinesischen Entwickler, die wie wir in einer hierarchischen Struktur arbeiten, bekommen den Auftrag, ein Problem zu lösen. Von oben wird Druck aufgebaut. Und nun starten eine ganze Reihe von Problemen die nur sehr schwer in den Griff zu bekommen sind. Der Prototyp liegt auf dem Tisch und muss unverzüglich auf den Prüfstand aufgespannt werden. Tests müssen durchgeführt und Testergebnisse visuell aufbereitet werden. Noch immer fehlen auf Arbeitsebene Lastdaten. Daher können keine sinnvollen Lastkollektive abgeleitet werden. Trotzdem muss ein Prüflauf mit dem schnell aufgebauten Prototyp stattfinden, damit die Erwartungen der höheren Managementebene erfüllt werden.
Es werden also Prüfläufe ohne Zweck und Ziel gestartet. Der erste Prototyp hält am Prüfstand bei weiten nicht so lange, wie geplant. Oft können Funktionalitäten nicht wie vorgegeben abgebildet werden. Die Ergebnisse der Prüfläufe bringen keine neuen Erkenntnisse. Und ab jetzt wird in vielen Fällen eine Spirale des Chaos ausgelöst. Ohne ausreichende Ursachenanalyse wird ein neuer Prototyp designed und gefertigt. Dieser zweite Prototyp wird auf den Prüfstand aufgespannt, obwohl noch immer Eingangsgrößen für sinnvolle Prüfläufe fehlen. Daher wird ein willkürlich definiertes Lastkollektiv auf den Prüfling gefahren, der wiederum vorzeitig versagt. usw. usf.. Die Kosten für die Produktion der Prototypen und Prüfstandstests explodieren.
Befinde ich mich nun in einer Projektphase, in welcher die Freigabe der nächsten Baustufe erfolgen und/oder auch schon die Beschaffung der Serienwerkzeuge ausgelöst werden muss, wird es kritisch. Die Entwicklungsreife des Bauteils oder der Komponenten entspricht nicht den Anforderungen. Man war zwar schnell, aber die Entwicklungsergebnisse sind bei weitem noch nicht ausreichend genug, um über einen Design-Freeze sprechen zu können. Trotzdem werden Werkzeuge ausgelöst und die Integration unreifer Komponenten oder Teilsysteme in das Gesamtsystem vorangetrieben.
Es ist erstaunlich, aber offenbar ist diese Entwicklungsphilosophie in China darstellbar. In Europa wäre diese Trial-and-Error-Methode ökonomisch nicht darstellbar. Die Konstruktion und Produktion der Prototypen allein würde Unsummen verschlingen, ganz zu Schweigen von den Kosten für Prüfläufe und die Validieren der Testergebnisse mittels Simulation. Dennoch jedoch geht die Botschaft der schnellen Prototypen und hohen Prüfsequenzen nach Europa, sofern vorhanden sogar in das EU-Headquarter der Automobilzulieferer und wird von da wie in einer Echokammer an die Belegschaft und Öffentlichkeit verstärkt.
Diese chinesische Entwicklungsphilosophie steht also konträr zur europäischen, die auf sehr hohen Entwicklungsstandards zurückgreifen kann. Ich habe in einem meiner Blogs zuvor schon einmal diese Graphik verwendet (siehe unten) und nehme diese nochmals her, um den europäischen Entwicklungsansatz zu beschreiben.
Um Kosten zu sparen muss ich mir im Vorfeld alle Details zu dem Produkt zusammentragen und möglichst viel sehr früh im Entwicklungsprozess in der Simulation abdecken. Dieses Vorgehen wird auch als Frontloading bezeichnet. Für eine sinnvolle lastdatenbasierte Simulation benötige ich sehr gute Belastungsdaten und wenn möglich validierte Festigkeitsmodelle meiner Bauteile. Habe ich das nicht, stolpere ich meist von einem Bauteilausfall zum Nächsten. Jeder Fehler, jede Unwissenheit vorher in der Simulation und später in der Erprobung bestraft letztendlich jeden Projektleiter später mit überhöhten Entwicklungskosten.
Schnelligkeit ist ok, aber ich muss den richtigen Zeitpunkt wählen, ab dem ich dann wirklich durchstarte und im Zuge der Entwicklungstätigkeiten hohe Kosten verursache.
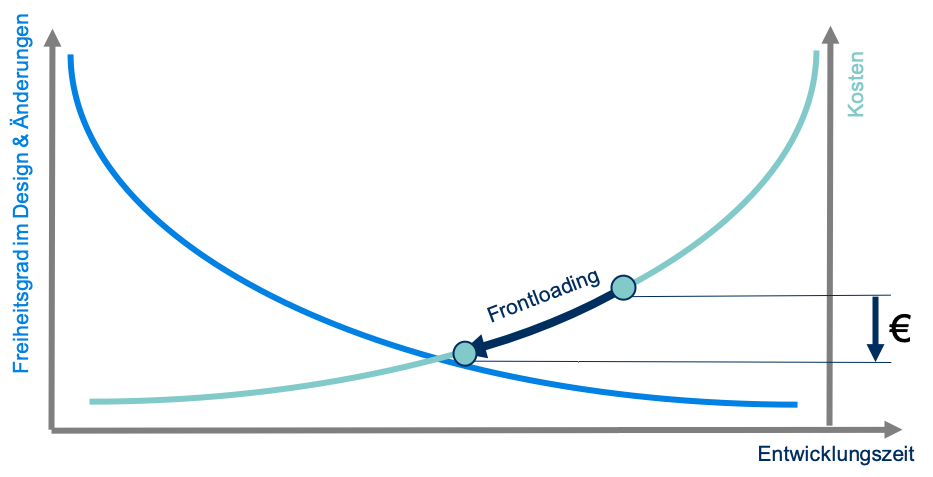
Die Botschaft hier ist: Es ist nicht die Geschwindigkeit der entscheidende Parameter, sondern im Vorfeld die Zeit zu investieren die ich benötige um meine Komponente so zu dimensionieren und zu berechnen, dass sie den geforderten Belastungen standhält. Jede Erkenntnis, jede Erprobung zu einem späteren Zeitpunkt verursacht in der Entwicklung wesentlich höhere Kosten.
Ich muss jetzt aber schon auch zugeben, dass die europäische Fahrzeugentwicklung es in den letzten Jahren übertrieben und Standards entwickelt hat, mit denen sie sich selbst im Weg steht. Hinzu kommen die EU Richtlinien und Berichtspflichten, höchste Sicherheitsstandards, Normen, Zertifizierungen usw.. Alle diese Aufgaben sind neben der Entwicklungstätigkeit zu erledigen und schlagen sich letztendlich auch in den Produktkosten nieder. Wenn diesem Trend in der EU nicht Einhalt geboten wird, wird es sehr schwierig werden hier konkurrenzfähige Produkte zu entwickeln und das bei ständig steigender globaler Konkurrenz.
Aus meiner Sicht täuschen manche chinesische Marken, vor allem die Newcomer OEMs, mit tollen Fzg-Features über minderwertige Qualität der Hardware hinweg. Viele Konsumenten lassen sich damit Ködern indem sie nur die Bildschirme im Fahrzeug. sehen und wieviel Heimkino das Fahrzeug bietet. Aber hält ein chinesisches Fahrzeug bei einer Nutzung so wir es gewohnt sind 300.000km, so wie es bei uns mittlerweile üblich ist und wie wir es gewohnt sind? Da stellt sich natürlich auch die Frage haben wir es mit den 300.000km übertrieben? Und wird das Auto ein Wegwerfartikel wie ein Handy? Nach 5 Jahren und 100.000km kommt es in den Müll? Und macht das für unsere Umwelt Sinn? Wie entwickeln sich auch die Gebrauchtwagenpreise von chinesischen Autos? Aktuell, so scheint es mir, haben viele der EU Konsumenten damit kein Problem. Wichtig für sie ist die Reichweite, die Anschaffungskosten, die Connectivity und die vielen Bildschirme.
Dieser Artikel gibt lediglich einen kleinen, sehr persönlichen Einblick in die chinesische Fahrzeugentwicklung gibt, basierend auf der Erfahrung mit wenigen chinesischen OEMs, zumeist Newcomer. Lassen Sie sich nicht verleiten, aus diesem Erfahrungsbericht allgemeingültig Aussagen abzuleiten. So, wie es auch in Europa mehr oder weniger reife OEM’s gibt (VW, BMW, INEOS), gibt es auch im riesigen Markt China’s höchst-kompetente OEMs, die bald schon an der Weltspitze stehen werden. Von diesen können wir hier in Europa viel lernen. Da bin ich sicher!
Um jetzt zum Schluss nochmal zum eigentlichen Thema zurückzukommen: Ich bin der Meinung, dass sie Entwicklungskosten in China aufgrund der unterschiedlichen Ansätze nicht viel geringer sind als bei uns. Mit Sicherheit sind sie in der Produktion der Fahrzeuge günstiger, da sie dort unter ganz anderen gesetzlichen, wirtschaftlichen und sozialen Rahmenbedingungen produzieren können als wir hier in Europa. Wichtig wäre es, dass so ein Gesamtbild der unterschiedlichen Entwicklungsstrategien beim obersten Management ankommt, um speziell in der europäischen Fahrzeugindustrie nicht das erarbeitete Know How und die Arbeitsplätze zu verlieren.
Lassen Sie uns mit den Chinesen in gesunder Konkurrenz bleiben, und lassen Sie uns nicht den vergessen, welchen Anspruch wir in der EU an ein Fahrzeug bezüglich Qualität und Langlebigkeit haben. Ich bin der Meinung, dass wir in Europa mit unserer Entwicklungsphilosophie, den eingespielten Prozessen und den Erfahrungen wettbewerbsfähig sind und uns nicht die Preisführerschaft anstreben sollten, um auf dem Weltmarkt zu bestehen.
Aber wir sollten auch darüber nachdenken, ob wir in Europa wirklich alle Richtlinien, Gesetze und Vorschriften brauchen. Ich habe noch niemanden getroffen der mir gesagt hat, er hat diese Fahrzeugmarke gewählt weil dieser Hersteller das Lieferkettengesetz am besten eingehalten hat.
Unsere Wettbewerbsfähigkeit entscheidet sich auch in den Dimensionen Rohstoffe, internationale Zusammenarbeit und Bürokratie.