Ich habe hier auf dieser Seite schon öfter über die Prüfmethodik von Getrieben bzw. Antriebssträngen, den dazugehörigen Prüfständen und auch über das Prüfcenter an sich berichtet. Heute möchte ich etwas tiefer über den Prüfstand selbst, d.h. über die Nutzung und Stillstände, sowie einer möglichen technischen Zukunft der Prüfstände berichten. Und ich möchte meine Gedanken teilen, wie ich die Zukunft dazu aktuell einschätze.
Mit der Elektromobilität, so denke ich, wird sich der mechanische Aufbau eines Prüfstandes schrittweise vereinfachen. Zwar wird man weiterhin den Elektromotor und das Getriebe separiert und auch gemeinsam erproben. Aber im Vergleich zu einem Antriebstrang mit Verbrennungsmotor in Verbindung mit einem automatisierten Getriebe in Hybridausführung und dann auch noch in einer Allradkonfiguration mit geregeltem AWD System aufzubauen, ist der reine E-Antrieb, rein mechanisch betrachtet, sehr viel einfacher darzustellen.
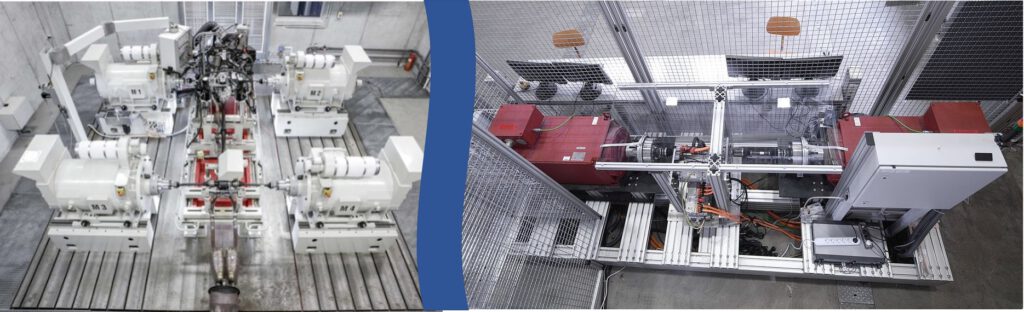
Wie auch immer der Aufbau aussieht: ein Thema ist immer die effektive Nutzung des Prüfstandes. Denn nur wenn der Prüfstand, sprich: wenn die Erprobung läuft, ist der Prüfstand produktiv. Produktiv in dem Sinne, als dass er zum einen Messdaten und Funktionsergebnisse, und zum anderen Schädigungseinträge in die zu erprobenden Bauteile liefert. Die durch den Aufbau oder den Stillstand verursachen Kosten sollten ist so gering wie möglich gehalten werden. Sind Kostenrechner und Wirtschaftlichkeitsexperten mit im Boot, heißt es ganz schnell „So ein Prüfstand muss 24 Stunden über 7 Tage non-stop laufen!“.
Wie schon erwähnt ist der mechanische Aufbau bei der Elektromobilität geringer. Nicht zu unterschätzen jedoch sind die Komponenten, die für den Betrieb und die Ansteuerung der E-Maschine(n) erforderlich sind. Und bei diesen gibt es eine ganze Menge Parameter die während des Prüflaufes stabil gemessen werden müssen. Um so mehr Parameter an den einzelnen Komponenten gemessen werden müssen, um so größer ist der Aufwand der Messtechnik selbst, wie auch die Implementierung dieser Messdaten in den Prüfstand.
Jede Messtechnik verhält sich in ihrer Eigenschaft, Messdaten zu liefern, anders. Das eine System liefert eine Spannung, das andere eine Frequenz und viele andere Sensoren sind mittlerweile in ein Bussystem integriert und leiten ihre Daten an Prozessoren weiter. Hier hätte ich mir für alles Messysteme ein Plug and Play System gewünscht, d.h. man steckt ein Messystem an der Schnittstelle zum Prüfstand an und die Messysteme liefern alle erforderliche Daten, aber auch Einstell- und Kalibrierparameter in das Prüfstandsmesssystem, um mehr oder weniger sofort mit den Messungen beginnen zu können. Wenn dann auch noch die Kalibrierprotokolle bei den Messdaten automatisiert abgelegt sind, dann wäre man sehr gut für jedes Audit gerüstet.
Ja, das gibt es schon teilweise, aber leider nicht vollständig und wenn, dann meist nur von einem Prüfstandsanbieter der mit einem bestimmten Messsystemhersteller zusammenarbeitet oder selbst Messsysteme herstellt.
Nicht nur die Integration der Messtechnik kann sehr viel Zeit in Anspruch nehmen. Auch die Inbetriebnahme des Prüfstandes selbst – und ich meine damit die ersten Phasen, wenn der Prüfstand sich zu drehen beginnt und Leistung in das System eingebracht wird – kann massive Verzögerungen verursachen. Passt jetzt die Dynamik zwischen den Antriebs- und Abtriebsmaschinen nicht zueinander, treten Schwingungen auf, die einen Betrieb ohne parasitären Schädigungseintrag unmöglich machen.
Jetzt wird lange an dem PID-Regler der Maschinen „herumgedreht“ um die Schwingungen in den Griff zu bekommen und das bei sehr vielen Drehzahl- und Momenten-, sprich Leistungspunkten. Das Ganze ist ein nicht zu unterschätzender Aufwand, wo mitunter daran mehrerer Ingenieure, länger als gewollt, arbeiten müssen.
Was ich hier zum Ausdruck bringen möchte ist, dass neben einem komplexen mechanischen Aufbau auch die Inbetriebnahme eines Prüfstandes sehr viel Zeit in Anspruch nimmt und somit die Nutzungsdauer reduziert. Alles was hier standardisiert und automatisiert umgesetzt werden kann, ist enorm hilfreich und letztendlich auch zukunftsorientiert.
Natürlich hängt das Ganze von weiteren Parametern ab. Habe ich einen oder mehrere Prüfstände, habe ich mehr oder weniger immer denselben Antriebsstrang erproben, wo alles schon eingestellt ist. Wenn das der Fall ist, wie bei OEMs meist üblich, könnte man relativ rasch nach dem mechanischen Auf- Umbau auf den Knopf drücken und starten. In den USA habe ich zum Beispiel mal einen Allradprüfstand gesehen bei sich die Abtriebsmaschinen an der Hinterachse automatisch an den kurzen oder langen Radstand der Antriebsstrangkonfiguration über Spindelantrieb und Schienen anpassen konnten und praktisch kein Umbau erforderlich war. Allzu oft wird dann von „Laien“ oder „Kostenfüchsen“ gesagt: „Die anderen können das viel schneller“.
Sprechen wir jedoch von einem Entwicklungsdienstleister, der viele unterschiedliche Kunden bedienen muss, sind diese Prüfstände möglichst flexibel zu gestallten und jeder Umbau ist mit viel Zeit und langen Stillständen verbunden.
Eines kann ich mit Gewissheit sagen, da schon mehrfach mit Kostenverantwortlichen diskutiert und aufgezeigt: Je flexibler ein Prüfstand ausgeführt ist, umso aufwändiger sind die Umbauten. Das ist ein ganz komplexes Thema das sehr viel Erfahrung benötigt. Aber auch das was ich in der Zukunft mit einem Prüfstand abdecken möchte ist hier extrem wichtig zu berücksichtigen.
Um jetzt noch einmal auf das eigentlichen Thema zurückzukommen; wie kann ich meine Inbetriebnahmezeit im Allgemeinen reduzieren?
Oben habe ich schon erwähnt; alle Messsysteme die ich benötige ohne langes Parametrieren mittels Plug and Play einfach „anstecken“ und für das hier beispielhaft beschrieben Schwingungsproblem einen selbst lernenden Prüfstand.
Was ich damit meine ist, dass der Prüfstand mir die gesamte PID-Regelungsanpassung im einem sog. „Kalibrierlauf“ abnimmt und anhand der ihm vorgegebenen Toleranzen sie selbst optimiert.
In der gesamten Unterhaltungselektronik ist das fast schon zu 100% Standard. Wer in den 80er Jahren einen Drucker an seinem PC angeschlossen hat kennt das Problem noch mit der Installation des dazugehörigen Treibers. Mit der Einführung der USB Schnittstelle konnte man so gut wie jedes Gerät „anstecken“ und alles wird im Hintergrund angepasst und ist sofort nutzbar.
Für einen Prüfstand der Zukunft wäre so ein integrierter Automatismus extrem hilfreich um den Nutzungsgrad eines Prüfstands zu erhöhen.
Wichtig ist auch für den Testcenter Verantwortlichen die genauen Laufzeiten und Stillstandszeiten zu dokumentieren und Kennzahlen (KPIs) zu schaffen.
Das ist insofern wichtig um die Stillstandszeiten zuordnen zu können. Vielfach liegt es nicht am Prüfstand selbst sondern am noch nicht ausgereiften Produkt welches erprobt werden soll oder auch an dem mangelnden Support der anderen Abteilungen oder Kollegen. Es wird oft sehr schnell die Aussage getroffen: „Der Prüfstand steht schon wieder“.
Auch hier könnte im Prüfstand neben der Steuerungssoftware ein Tool von Hilfe sein, dass bei der Erstellung und Auswertung von KPIs unterstützt.
Umfangreiches Wissen und Erfahrung sind vonnöten um hier vorne dabei zu sein.
Sinamono kann dazu mit den vorhandenen Experten eine adäquate Unterstützung anbieten um Dienstleister, Zulieferer aber auch OEMs in ihren Aufgaben zu unterstützen.