Ich habe schon mehrere Artikel über das Testen und die Testmethoden für die Entwicklung von Komponenten im Antriebsstrang in PKW Anwendungen hier veröffentlicht. In diesem Artikel möchte ich mehr über die Anforderungen an das Testcenter, d.h. das Gebäude und die notwendige Infrastruktur für den Prüfstandsbetrieb eingehen.
Der technische Aufwand für das Testcenter hängt natürlich von sehr vielen Faktoren ab. Wesentliche Faktoren sind Komplexität der eingesetzten Prüfeinrichtungen, aber auch von der Größe und die Art der Prüfstände. Das kann mit der Prüfung von einzelnen Getriebekomponenten beginnen und beim Einbringen eines gesamten Fahrzeuges in die Prüfzelle enden. Natürlich darf auch der Platzbedarf der etwaigen Nebenaggregate wie z.B. Fahrtwindkühlung, Temperaturkonditionierung für diverse Betriebsstoffe aber auch der Bedarf der zusätzlichen Messtechnik und Steuerungen nicht vergessen werden. Es kann auch der Fall eintreten, dass zusätzliche Aktuatoren zum Bedienen mechanischer Systeme aufgestellt werden müssen.
Eines möchte ich hier gleich vorwegnehmen, je multifunktionaler, d.h. für unterschiedlichste Aufbaukonfigurationen der Prüfstand verwendbar ist, umso aufwändiger und zeitintensiver sind die Umbauten und Inbetriebnahmen von einem Projekt zum anderen. Hier ist vor allem das Rüsten gemeint, da meist alles in der Prüfzelle umgebaut, sprich umgestellt und neu eingestellt werden muss.
Ein Zulieferer, ein TIER1 der viele Kunden bedienen muss ist mehr oder weniger gezwungen die Variante eines multifunktionalen Prüfstandes zu wählen. Ein OEM der seine Standard Antriebstränge prüft kann sich mehr oder weniger auf eine Fahrzeug-Plattform konzentrieren und passt nur wenige geometrische Einstellungen, wie z.B. den Achsabstand, an. Natürlich kommen noch viele andere Faktoren hinzu, aber dieses Beispiel bringt den Unterschied schnell auf den Punkt.
Dieser Unterschied ist jemanden der mit der Thematik nicht so vertraut ist oft schwierig zu erklären, vor allem dann wenn die Technik und die Finanz über das Thema Kostenoptimierungen und Prüfstands – Stehzeiten diskutieren.
Umso mehr ich auf die „Palette“ packe umso schwerer wird diese und umso höher kann diese auch werden, was das Einbringen erschwert. Viele Prüfstandshersteller haben sich schon sehr umfassenden dem Thema angenommen und die Lösung beim Rüsten liegt meist in einer Vormontage der Komponenten außerhalb des Prüfstandes, und diese dann so weit wie möglich vorinstalliert in die Prüfzelle einzubringen. Hier spricht man meist von sog. Palettensystemen die dann quasi vormontiert in den Prüfstand eingebracht werden. Teilweise ist es auch möglich bei komplexen Systemen diese schon vorab auf der Palette in sog. Vorbereitungsräumen in Betrieb zu nehmen. Wichtig ist in jedem Fall die Montagefläche für den Prüfstand, hier empfiehlt sich auf jeden Fall sog. Nutplatten zu verwenden die fast die gesamte Bodenfläche der Prüfzelle ausfüllen sollten. Sind auch geeignete Kräne vorhanden um die Lasten zu bewegen?
Wo sitzen auch meine Supportabteilungen, wie z.B. die Messtechnik, der Prototypenbau, die Elektroniker usw.?
Wichtig ist es auch diese in unmittelbarer Nähe zu haben, um rasch bei Störungen unterstützen zu können.
Natürlich spielt hier die Beschaffenheit des Gebäudes eine ausschlaggebende Rolle. Ist der Gangbereich groß genug, ist die Prüfzelle für die Aufgabe geschaffen, habe ich alle Betriebsstoffe und Medien verfügbar um die Prüfungen durchzuführen usw.? Wo und wie erfolgt meine Zulieferung der benötigten Teile?
Habe ich in meiner Gebäudeplanung alle „Betriebsstoffe“ zur Verfügung? Hier einige Beispiele von einem Antriebsstrangprüfstand:
Ist ausreichend Strom für die Antriebsmaschinen und auch ausreichende Stromrückführung um diese im Generatorbetrieb zu betreiben vorhanden, eine ausreichende Raumbelüftung um die Verlustwärme abzuführen, Kaltwasser um die Antriebsmaschinen zu kühlen? Nun aktuell für die E-Mobilität ist ausreichend Strom vor allem Spannung (mind. 800V) um die E-Maschinen zu betrieben vorhanden? Muss auch klimatisiert werden um eine bestimmte Umgebungstemperaturen für die geforderten Prüfungen einstellen zu können?
Und dann kommt noch ein ganz entscheidender Faktor hinzu, das ist die Kabelverlegung vor allem in der Prüfzelle. Wer sich mit dem Thema EMV (Elektromagnetische Verträglichkeit) noch nicht beschäftigt hat kann hier vor einer unlösbaren Aufgabe stehen. Die Ursachen dafür sind sehr vielschichtig, für den Laien ein Beispiel dazu: Vorhin habe ich von 800V gesprochen die für die E-Maschinen benötigt werden, aber die Messtechnik die auf dem Prüfstand verbaut wird arbeitet im mV Bereich. Vieles wird mittlerweile in der Messtechnik schon digital oder als Frequenz übertragen, aber leider nicht jede Messtechnik und somit nicht alle Signale. Und wenn ich nun EMV Störungen in meinen Messleitungen habe werde ich mit meinem Prüfergebnis nicht zufrieden sein.
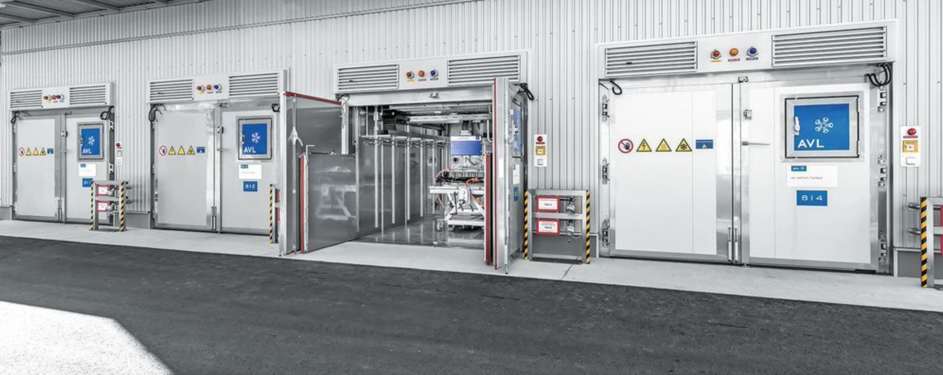
Nun auch zum Raumbedarf:
Meine Erfahrung zeigt, dass für den Betrieb eines komplexen modernen Antriebstrang-Prüfstandes mit ca. 10.000€/m2 für die Herstellung eine adäquate Prüfzelle inkl. der dazugehörigen Prüfstandsinfrastruktur kalkuliert werden kann. Somit ist es wichtig den Raumbedarf so kompakt wie möglich zu planen. Mittlerweile hilft auch die neue Technik Platz zu sparen, den in der Vergangenheit musste der Prüfstandsbediener unmittelbar neben dem Prüfstand platziert und dieser konnte mittels eines Panzerglas gesicherten Fensters den Prüfstand beobachten. Heute kann man das mit Kameras bewerkstelligen und ich kann den Bediener etwas vom Geschehen wegplatzieren und die Raumgestaltung etwas anders Planen.
Ein weitere „Platzfaktor“ ist das sog. Zubehör für die Montage, Betrieb, Messtechnik usw. Ich kenne einige Firmen die das über eine ausgeklügelte Logistik aus den Prüfräumen heraushalten. D.h. alles was nicht täglich gebraucht wird, wird in einem Logistiklager gelagert und nimmt keinen teuren Platz im Testcenter ein. Natürlich muss hier eine Logistikinfrastruktur vorhanden sein die eine tägliche, vielleicht in Ausnahmefällen eine ½ tägliche, Zugriffszeit auf die angeforderten Teile gewährleistet und diese innerhalb dieser Zugriffszeiten vor Ort liefert bzw. abholt. Neben mehr Platz in meinem Testcenter schaffe ich damit auch gleichzeitig mehr Ordnung.
Wichtig ist auf jeden Fall für die Auslegung und Planung des Testcenters der sog. „Materialfluss“.
Wer hier schon vieles was er für seine zukünftigen Aufgaben berücksichtigen kann legt schon zu Beginn einen großen Grundstein zur Effizienz im späteren Betrieb. Es sollte hier nicht der Billigstbieter beauftragt werden, bitte greifen sie auf einen erfahrenen Planer zurück die sich damit schon mehrmals beschäftigt haben. Glauben sie mir das rechnet sich in wenigen Jahren, vielleicht sogar in Monaten. Testcentren die wachsen bzw. ausgebaut werden habe meist Haken und Ösen die nicht mehr so leicht wieder wegzubekommen sind.
Ich habe beides erlebt, und ein Neubau kann mitunter die billigere Lösung sein, vor allem wenn man auf einen längerfristigen Businessplan zurückgreifen kann.
Es wird immer versucht einen 24 Stundenbetrieb über 7 Tage anzustreben, denn ein nicht genutzter Prüfstand ist schließlich totes Kapital. Um das aber realisieren zu können muss ich mir zuvor in der Planung schon sehr intensiv mit all den genannten Einflussfaktoren beschäftigen.
Umfangreiches Wissen und Erfahrung sind vonnöten um hier vorne dabei zu sein.
Sinamono kann dazu mit den vorhandenen Experten eine adäquate Unterstützung anbieten um Dienstleister, Zulieferer aber auch OEMs in ihren Aufgaben zu unterstützen.